Intake Manifolds: Understanding Their Design and Performance
Intake manifolds are essential components in internal combustion engines. They distribute the air-fuel mixture to the engine's cylinders, influencing performance and efficiency. The design of intake manifolds has evolved over time, leading to various types and materials. Understanding their function and construction is key to optimizing engine performance and addressing maintenance needs.
Understanding Intake Manifolds
The significance of intake manifolds in engine mechanics cannot be overstated. This section delves into their definition, role, historical development, and innovations within this crucial automotive component.
Definition and Role in Engines
Intake manifolds serve as the vital link between the engine's air supply and its combustion process. Their primary function is to distribute the air-fuel mixture evenly to each cylinder, which is essential for optimal engine performance. A well-designed manifold enhances the engine's ability to breathe effectively, improving both power output and efficiency.
Key functions of intake manifolds include:
Even distribution of the air-fuel mixture.
Creation of a vacuum for various vehicle systems.
Support for critical components like carburetors and fuel injectors.
Historical Development and Innovation
Intake manifolds have undergone significant evolution since the advent of internal combustion engines. Initially crafted from cast iron, these components have transitioned to lightweight aluminum and advanced plastic composites to improve performance and efficiency.
Innovations over the years include:
Enhanced designs for better airflow dynamics.
Variable geometry systems that optimize performance across different RPM ranges.
Integration of modern materials that resist corrosion and reduce weight.
This progression reflects ongoing research and development aimed at maximizing the effectiveness of intake manifolds, contributing to enhanced vehicle performance in contemporary engineering.
Types of Intake Manifolds
Several designs of intake manifolds exist, each influencing engine performance and efficiency in different ways. Understanding these variations is essential for optimizing engine setups and achieving desired power outputs.
Single-Plane and Dual-Plane Design
Single-plane manifolds offer a simpler construction with a uniform airflow path, primarily used in high-performance applications. They provide excellent high-end power, ideal for racing. In contrast, dual-plane designs create two separate air passages for improved low-end torque and throttle response, making them suitable for street applications.
Variable Geometry Intake Manifolds
Variable geometry intake manifolds feature adjustable runners that change length based on engine speed. This adaptability enhances torque across a broader RPM range, allowing optimal performance for varying driving conditions. The ability to tune the airflow creates opportunities for more efficient combustion.
Temperature-Adaptive Intake Manifolds
Temperature-adaptive manifolds utilize heated gases or external heating elements to optimize fuel vaporization. This design is particularly beneficial in cold weather, ensuring better engine start-up and performance. By maintaining an ideal temperature, these manifolds help reduce emissions and improve fuel efficiency.
The choice of materials and manufacturing techniques for intake manifolds directly impacts their performance and durability. Various materials offer distinct advantages, contributing to the manifold's efficiency and responsiveness in engine operation.
Materials and Manufacturing
Aluminum and Cast Iron Manifolds
Traditionally, many intake manifolds are produced using aluminum or cast iron. Each material has unique properties that affect weight, heat management, and corrosion resistance.
Aluminum: Known for its lightweight nature, aluminum enhances engine efficiency by reducing overall weight. It also provides excellent thermal conductivity, which helps in maintaining optimal temperatures within the manifold.
Cast Iron: While heavier than aluminum, cast iron offers exceptional durability and heat retention. This makes it suitable for high-performance applications where stability is crucial. However, its weight can hinder performance in certain designs.
Plastic Composite Innovations
In recent years, advancements in materials have led to the increased use of plastic composites in the manufacturing of intake manifolds. These innovative materials provide unique benefits for modern engines.
Weight Reduction: Plastic composites are significantly lighter than metal options, aiding in overall vehicle efficiency and performance.
Corrosion Resistance: These materials exhibit superior resistance to corrosion, ensuring longevity and reliability in various environmental conditions.
Complex Designs: The malleability of plastics allows for more intricate designs, which can optimize airflow and improve engine efficiency.
The Role of Turbulence in Fuel Atomization
Turbulence plays a vital role in the atomization of fuel within an engine. It influences how fuel mixes with air, affecting combustion efficiency and overall engine performance.
Creating Turbulence for Atomization
Turbulence is induced in the intake manifold to enhance the mixing process of fuel and air. Effective atomization occurs when fuel droplets are broken into smaller particles, facilitating better combustion. Key factors in creating turbulence include:
Shape and design of the intake manifold
Placement of fuel injectors or carburetors
Engine speed and load conditions
Increasing turbulence improves the dispersion of fuel droplets, allowing for a more uniform mixture. This helps achieve more complete combustion, thus optimizing engine power and reducing emissions.
Balancing Turbulence and Pressure Drop
While turbulence is essential for effective atomization, it must be carefully managed to prevent excessive pressure drops within the intake manifold. High turbulence can lead to:
Reduced air flow into the combustion chamber
Lower overall engine efficiency
Therefore, designing manifolds involves finding the right balance between inducing sufficient turbulence for atomization and maintaining adequate pressure to support efficient airflow. This balance is crucial for achieving optimal engine performance while avoiding detrimental effects on power output and efficiency.
Enhancing Volumetric Efficiency
Volumetric efficiency is a critical factor in engine performance, crucially influenced by intake manifold design. Optimizing this aspect ensures that the right amount of air and fuel enters the engine for combustion, leading to enhanced power and efficiency.
Runner Design and Airflow Dynamics
The design of runners plays a significant role in determining airflow dynamics within the intake manifold. Runners must facilitate smooth and efficient airflow to ensure optimal fill of the combustion chambers. Factors influencing runner design include:
Length: Longer runners can enhance low-end torque by utilizing intake pulse dynamics but may sacrifice high RPM performance.
Shape: Contours must minimize turbulence while maintaining sufficient velocity to support effective charging of the cylinders.
Straight vs. Curved: Straight runners generally provide less resistance, whereas curved runners can help manage airflow direction for better efficiency.
Helmholtz Resonance and Timing Optimization
Helmholtz resonance occurs in intake systems, impacting air pressure and velocity during engine cycles. Achieving optimal timing for valve operation is crucial. Effective synchronization enhances the natural resonant frequencies of the intake, improving filling efficiency. Key considerations include:
Runner length tuning to match desired RPM ranges.
Using velocity stacks to amplify airflow at specific engine speeds.
Applications in Naturally Aspirated Systems
Naturally aspirated systems particularly benefit from enhanced volumetric efficiency as they rely solely on atmospheric pressure for air intake. Innovations in manifold design and runner configuration can lead to notable gains in performance. Critical applications include:
Improved intake port geometry to support higher airflow.
Optimized throttle response for better drivability.
Impact on Engine Performance
The design of intake manifolds significantly influences engine performance, affecting both torque and power outputs as well as overall engine packaging. Optimizing these components leads to enhanced engine efficiency and driving experience.
Torque and Power Considerations
Intake manifolds play a vital role in determining the torque and power characteristics of an engine. The shape and length of the runners and their arrangement directly influence airflow and mixture distribution, essential for combustion efficiency. Key factors include:
Long runners typically enhance low-end torque by promoting better air-fuel mixture dynamics.
Short runners can improve high RPM power, allowing for faster air movement into the cylinders.
The intake manifold's design affects the engine's ability to maintain optimal combustion pressure, translating into greater power output.
Compact Designs and Engine Packaging
Modern engine designs require compact solutions, and intake manifolds are no exception. By optimizing the manifold's shape:
Manufacturers can reduce overall engine size, allowing for better integration into tight engine compartments.
Compact manifolds contribute to lower vehicle weight, enhancing fuel efficiency and handling.
A smaller footprint facilitates better thermal management, improving engine performance across various operating conditions.
Thus, the innovative design of intake manifolds is essential for maximizing performance and maintaining efficiency in contemporary automotive engineering.
Frequently Asked Questions About Intake Manifolds
This section addresses common queries related to intake manifolds, providing insights into their applications in popular vehicles and comparative performance across different brands.
Air Intake Manifolds in Popular Vehicles (LS, 5.7 Hemi, SBC)
Various vehicles employ distinct intake manifold designs to enhance engine performance. Below are notable examples:
LS Engines: Known for their efficient airflow dynamics, LS engines utilize a compact and lightweight manifold that improves horsepower and torque.
5.7 Hemi: The 5.7 Hemi features a unique intake design that promotes better fuel atomization and improved throttle response, making it popular in trucks and performance cars.
SBC (Small Block Chevy): Renowned for its versatility, the SBC's manifold options range from single-plane to dual-plane designs, catering to different performance needs.
Comparing Performance in Ford, Mazda, Subaru, Mercedes-Benz
Performance variations in intake manifolds can be observed across different automobile manufacturers:
Ford: Ford's EcoBoost engines utilize turbocharged setups with specially designed manifolds that enhance responsiveness and efficiency.
Mazda: Known for their Skyactiv technology, Mazda integrates lightweight manifolds that optimize combustion for better fuel economy.
Subaru: Subaru's boxer engines feature unique manifold layouts that deliver a low center of gravity while providing balanced power output.
Mercedes-Benz: Utilizing advanced engineering, Mercedes-Benz’s intake manifolds often feature variable geometry designs, optimizing performance across various RPM ranges.
Proper maintenance of manifolds is essential to ensure optimal engine performance. Several common issues can arise, affecting functionality and efficiency.
Common Issues and Maintenance of Manifolds
Detecting and Resolving Malfunctions
Several indicators can signal problems with the intake manifold. Common symptoms include:
Decreased engine performance and acceleration
Unusual engine noises, like hissing or sucking sounds
Engine misfires or rough idling
Check engine light illumination
To diagnose these issues, visual inspections are crucial. Look for visible cracks, vacuum leaks, or any signs of wear. Utilizing diagnostic tools can also help identify performance problems, enabling timely repairs.
Best Practices for Maintenance
Regular maintenance can considerably prolong the life of the manifold. Key practices include:
Routine inspections to check for signs of damage or wear
Cleaning the manifold periodically to prevent carbon buildup
Ensuring proper sealing and gaskets to avoid leaks
Replacing worn or damaged components promptly to avoid further issues
Implementing these maintenance practices helps maintain optimal performance and prevent costly repairs down the line.
Future Trends in Intake Manifold Technology
The field of intake manifold technology is witnessing significant advancements that promise to enhance engine efficiency and performance. With ongoing research and development, future manifolds are set to embrace new materials and designs as well as integrate with sophisticated fuel systems.
Emerging Materials and Design Innovations
Innovative materials are being introduced to overcome limitations of traditional aluminum and plastic composites. Current trends include:
Advanced Composites: These materials offer reduced weight and improved thermal properties.
3D Printing Technologies: This allows for more complex geometries and custom designs tailored to specific engine requirements.
Biodegradable Materials: Driven by environmental concerns, there's a push towards materials that reduce ecological impact.
Design innovations focus on optimizing airflow and thermal management, which enables better performance across various driving conditions. Moreover, adjustable manifolds that respond to engine demands are becoming prevalent.
Integration with Advanced Fuel Systems
The future of intake manifolds also involves tighter integration with hybrid and electric systems. Key developments in this area include:
Smart Manifolds: Equipped with sensors that monitor airflow and adjust accordingly to optimize combustion.
Direct Fuel Injection Compatibility: Enhancements to support more efficient fuel atomization and distribution.
Electronic Control Systems: Providing dynamic adjustments based on real-time engine performance data.
This seamless integration will likely improve overall engine responsiveness and efficiency, making vehicles more sustainable.
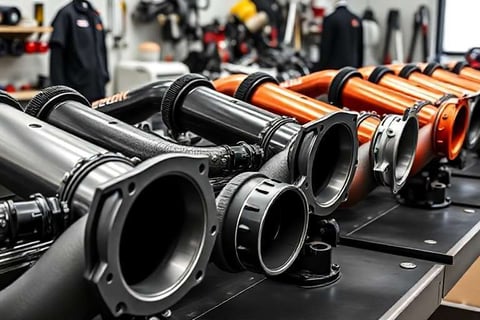
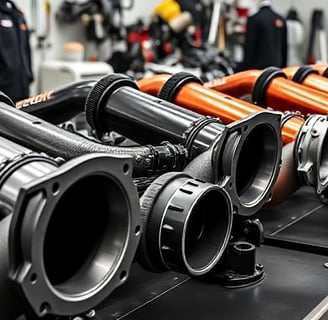
Motorsport
Experience exceptional racing with our expert guidance.
Rodiauto Sport LLC
500 4TH ST NW Suite 102
87102 Alburquerque - NM - US.
Advice
Services
info@rodiautosport.us
© 2025. All rights reserved.